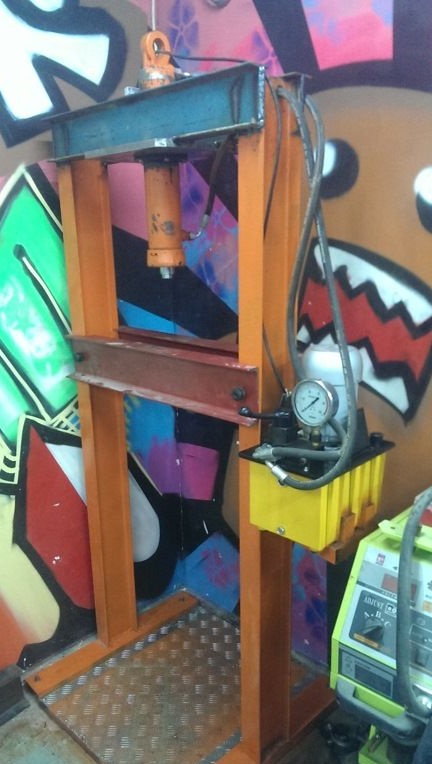
Der Anwendungsbereich von Hydraulikpressen ist recht groß: Sie können in Autowerkstätten zum Einpressen, Auspressen von Lagern, Zahnrädern, Wellen usw. verwendet werden. Sie werden auch zum Stanzen von Metallteilen, Pressen von Holzspänen, Kunststoff und Gummi verwendet. Fertige Maschinen kosten ab 100.000 Rubel. In diesem Artikel beschreibt der Autor eine recht kostengünstige und gleichzeitig hochwertige Konstruktion einer hydraulischen Presse, die eine maximale Kraft von 35 Tonnen pro 50 Quadratzentimeter liefern kann.
Zum Erstellen einer Maschine ist Zugriff auf die folgenden Geräte erforderlich:
- Drehmaschine;
- Bohrmaschine;
- Schweißvorrichtung.
Werkzeuge wie ein Schleifer und ein Bohrer werden ebenfalls benötigt.
Die zum Erstellen benötigten Materialien werden im Artikel selbst aufgeführt.
Bei der Herstellung des Maschinenrahmens ist es wichtig, besonders auf seine Festigkeit zu achten, da er enormen mechanischen Belastungen ausgesetzt ist. Die Metalldicke sollte hier ausreichen, um den vom Hydraulikzylinder ausgeübten Kräften standzuhalten und nicht zu verbiegen. Der Autor des Artikels verwendete 14 T-Träger als Basis. Daraus wird ein P-förmiger Rahmen gekocht, dessen Sockel unten aus dünneren Kanälen und Ecken besteht.
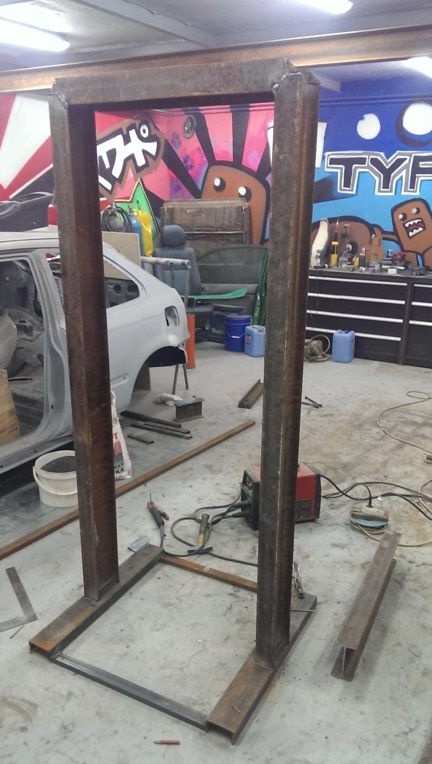
Ungefähr in der Mitte wird eine Arbeitsplattform aus zwei dicken Kanälen geschweißt:
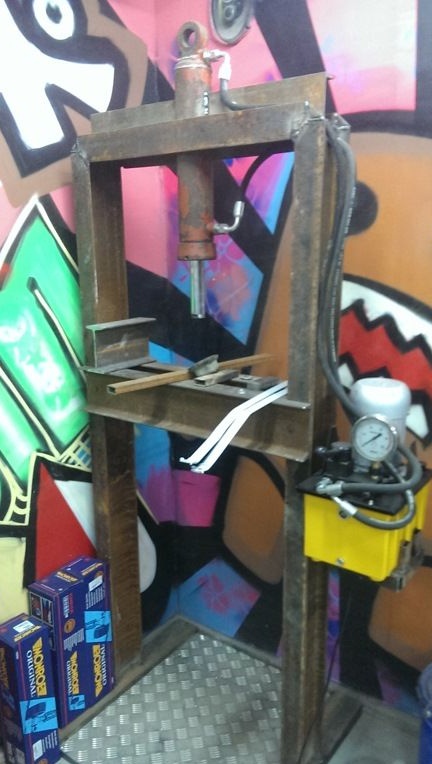
Anfangs verwendete der Autor eine andere Befestigung des Hydraulikzylinders, aber er erbrach sich aus dem Bett, so dass beschlossen wurde, einen neuen zu zerlegen und herzustellen. Wenn der Zylinder früher einfach mit dem Träger verschweißt wurde, wurde jetzt beschlossen, ihn durch den Flansch auf eine 20-mm-Platte zu pflanzen. Die Platte selbst befindet sich auf zwei T-Trägern.
Um den Zylinder in den Flansch zu setzen, wird der Zylinder auf einer Drehmaschine bearbeitet.
Hier ist die Ausgabe:
Der Flansch besteht aus einer Autonabe, die auf derselben Maschine bearbeitet wurde:
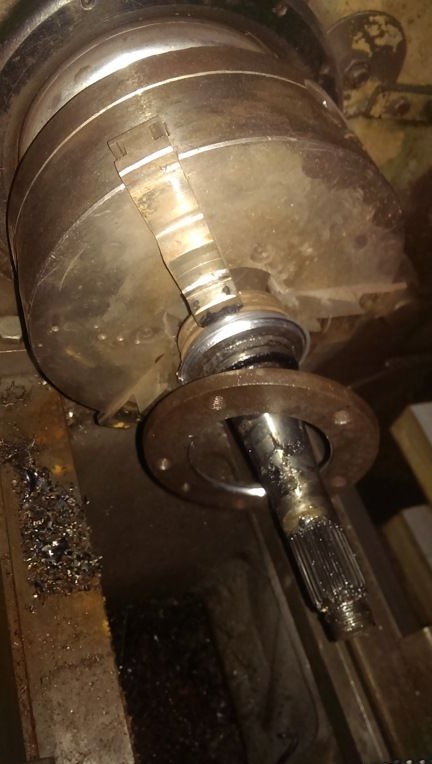
Dann wurde eine 20 mm dicke Metallplatte verwendet. Um ein Loch für einen Zylinder zu bohren, muss er irgendwie in der Maschine befestigt werden.Dazu wird ein runder Vorsprung in die Mitte der Platte geschweißt. Denn ihr Teller ist in der Maschine montiert.
Als nächstes folgen die Schweißarbeiten. Die Platte ist mit den Trägern verschweißt:
Der Flansch wird auf den Zylinder gelegt und im Kreis verbrüht:
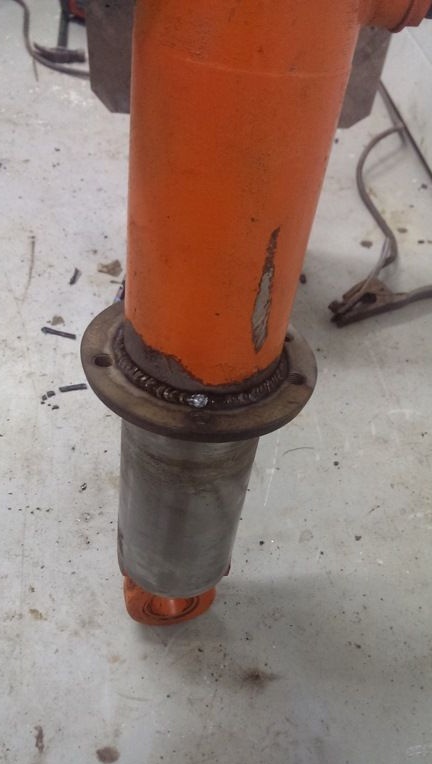
Damit der Zylinder gleichmäßig sitzt, wird die angrenzende Oberfläche des Flansches auf einer Drehmaschine bearbeitet:
Eine Platte mit daran angeschweißten Trägern wird an ihrer Stelle installiert und geschweißt:
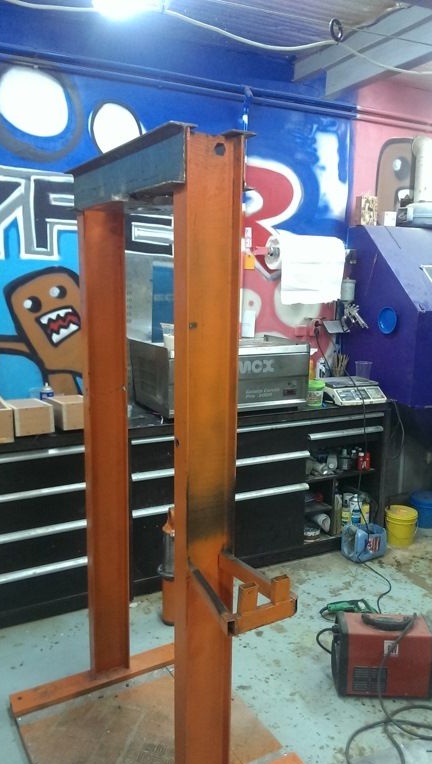
Ferner werden Löcher durch die Gegenlöcher der Nabe in der Platte gebohrt, durch die Befestigungsschrauben geführt werden.
Damit der Zylinder nicht nur an einer Stelle befestigt werden kann, wird ein weiterer Flansch bearbeitet, auf die Oberseite des Zylinders gelegt und mit den Trägern verschweißt.
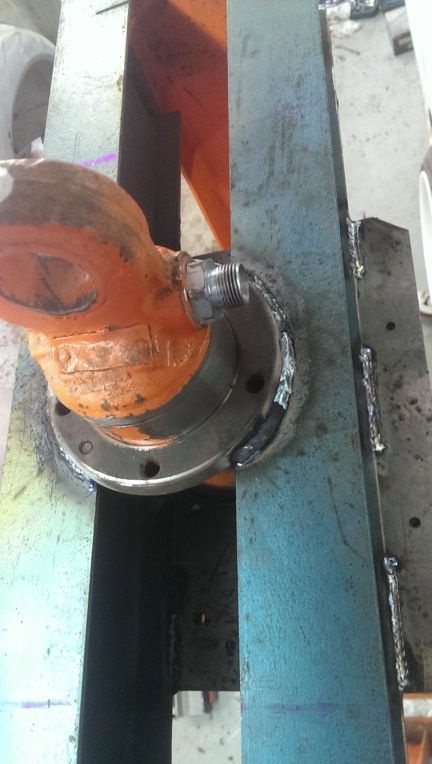
T-Träger im oberen Teil werden zusammengeschweißt und die Struktur ist fertig. Als nächstes wird eine Ölstation installiert, Schläuche versorgt und die Maschine ist bereit.
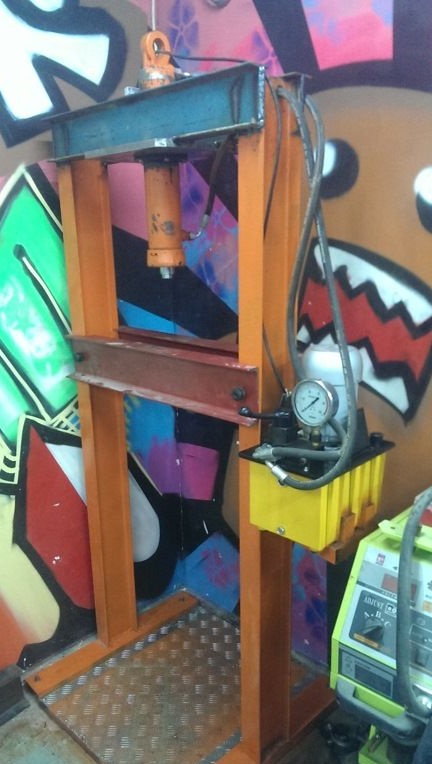