Die heutige Veröffentlichung widmet sich der Frage, wie einfach, schnell und mit einer minimalen Anzahl von Werkzeugen gearbeitet werden kann mit seinen eigenen Händen zuverlässiger und bequemer Verschluss.
Ich werde in der richtigen Reihenfolge beginnen.
Ich habe immer diese Schlösser und Verschlüsse auf Lager:
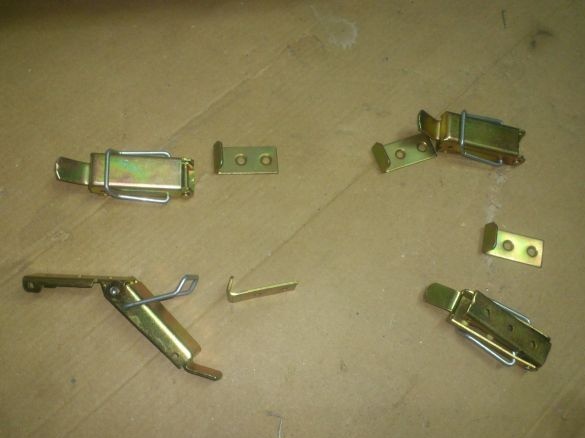
Sie werden in Geschäften verkauft, in denen Möbelzubehör verkauft wird, und heißen "Estrich für einen Schiebetisch" ...
Solche Befestigungselemente eignen sich nicht für "ästhetische" Produkte, sondern für "technogene" - das war's! ))) Weil sie selbst stark und zuverlässig sind und darüber hinaus ein sehr dichtes Widerlager der Abdeckung an der Basis bieten, da sie nicht nur eine "Verriegelung", sondern auch eine "Spannwirkung" haben))))). Bei hausgemachten Produkten ist dies besonders wichtig - mit ihrer Hilfe wird manchmal eine unzureichend genaue Passform ausgeglichen. Darüber hinaus wird dank des Designs bei ordnungsgemäßer Installation das versehentliche Öffnen praktisch vollständig vermieden!
Sie kosten nur ein paar Cent, und deshalb versuche ich gelegentlich, sie immer auf Lager zu kaufen ...
Mit ihnen repariere ich zum Beispiel die "Koffer" des Elektrowerkzeugs, wenn die "normalen" Kunststoffbefestigungen mit der Zeit abbrechen:
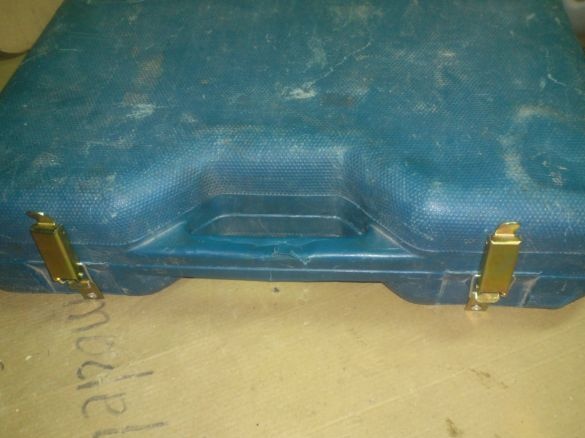
Und über hausgemachte Produkte und sag nein! Nur unter den auf dieser Site präsentierten habe ich sie in solchen Kreationen wie verwendet Box für das Schweißgerät :

Fall für Hausgemachtes Stativ :
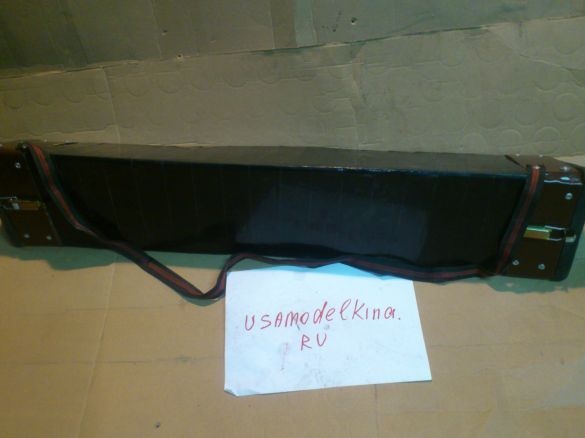
Thermoskanne für Zwei-Liter-Flaschen
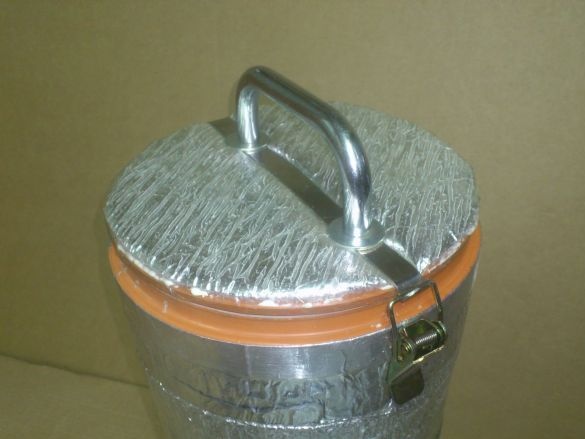
Und in einer Schublade für hausgemachte Gewinde Nietmaschine
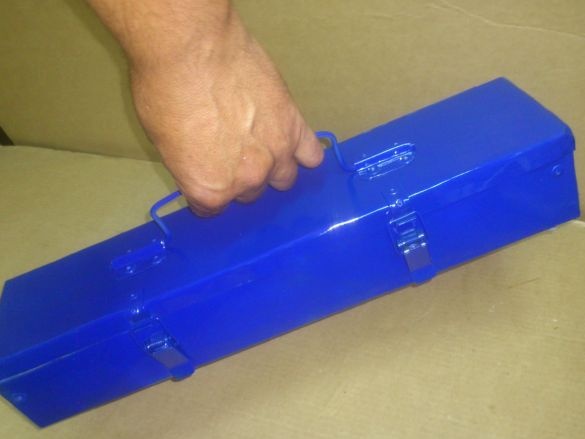
Und das wird nur hier veröffentlicht!
Im Allgemeinen ist ihr Anwendungsbereich ziemlich breit!
Bis jetzt hatte ich keine Ahnung, solche Estriche mit meinen eigenen Händen zu machen. Schließlich sind sie, wie ich bereits sagte, überhaupt nicht teuer, und es ist sinnvoll, etwas nur dann zu tun, wenn es entweder erhebliche Einsparungen bringt oder das resultierende Produkt einige Eigenschaften aufweist, die nicht im Kauf enthalten sind !!!
Und genau so ein Moment ist gekommen.)))). Während ich an dem nächsten hausgemachten Produkt arbeitete (das ich später vorstellen werde), wurde ich mit der Tatsache konfrontiert, dass ich sie angesichts ihrer Größe nicht verwenden kann. Ich muss die Verschlüsse an einer Stelle anbringen, die nur fünfeinhalb Zentimeter lang ist !! Und sie benötigen zusammen mit Haken viel mehr Platz ...
Nachdem ich das Möbelgeschäft angerufen hatte, stellte ich fest, dass es keine anderen, kleineren Größen gibt, und beschloss, einen Abend damit zu verbringen, sie herzustellen ...
Und hier ist, was ich dafür brauchte:
1. U-förmiges Aluminiumprofil, Abschnitt 10 x 10 cm (Zuschneiden).
2.Gehäusetrimmung von einem alten Computer-Netzteil.
3. Fahrrad sprach.
Ich muss sofort sagen, dass ich ursprünglich vorhatte, einfach alle Details aus der Dose zu biegen. Aber die Schnitte des Aluminiumprofils, die nach der Herstellung zurückblieben, fielen mir auf Armbrust
Und ich entschied, dass ich dieses Profil an die Spitze bringen würde. Dies spart nicht nur Zeit, sondern Aluminium wird in diesem Fall auch bevorzugt, da es leichter zu reinigen ist und die Wände dicker sind. Das Öffnen eines solchen Verschlusses wird also weniger wahrscheinlich zerkratzt.))))
Nachdem ich die Abmessungen des zukünftigen Produkts, das ich benötige, "geschätzt" habe, habe ich die Konturen des Profils mit einem Marker gezeichnet:
Und mit Winkelschleifer schneiden:
Danach habe ich die Grate abgelegt. Bei Aluminium ist dies sehr einfach. (Ich habe diesen Prozess nicht fotografiert)
Mit einer elektrischen Bohrmaschine und einer Bohrmaschine mit einem Durchmesser von 2 mm bohrte ich zwei Löcher in jede Profilwand - eines für die Achse, das zweite für den Federhaken:
Jetzt müssen Sie den unteren (festen) Teil des Estrichs machen. Es sollte ein "Graben" der gleichen Form sein, der in den ersten gehen sollte. Das fertige zu finden wird nicht funktionieren, also habe ich beschlossen, es aus der Dose zu biegen. Auf der Suche nach einem geeigneten Material stieß mein Blick auf das Gehäuse des alten Computer-Netzteils ... Genauer gesagt auf die Überreste des Gehäuses!))) Ich habe bereits Metall daraus geschnitten ... Es scheint, in der Herstellung Festplattenquadrat
Metall ist für meine Zwecke gut geeignet. Es ist weich genug, was bedeutet, dass es leicht zu verarbeiten ist! Und die Festigkeit und Steifigkeit der Struktur wird durch ihre Form bereitgestellt ...
Daraus schnitt ich einen Streifen der benötigten Größen aus und bog eine Rinne heraus. Als Dorn habe ich ein Stück Stahlblech geeigneter Dicke verwendet. (In meinem Fall - 6 mm.)
Markieren mit einem Marker, ich "schneide die überschüssige" Mühle ab.))))
Wie Sie, glaube ich, verstanden haben, muss diese Nut vollständig in das erste Aluminium passen. Als es dort passte, bohrte ich Löcher hinein und benutzte die Löcher im Aluminiumaußenteil wie eine Schablone ...
Jetzt können Sie die gesamte Struktur verbinden. Als Material für die Herstellung der Achse und des Federhakens habe ich eine Fahrradspeiche gewählt. Das alte Rad liegt in meinem Altmetall herum und hat mich mehr als einmal mit diesem Material versorgt.)))
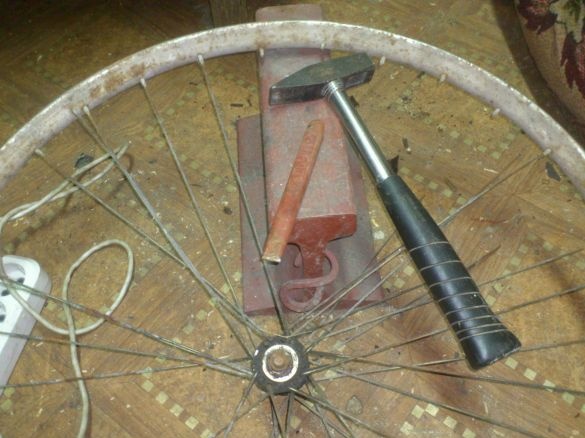
Fahrradspeichen bestehen aus ziemlich duktilem Stahl. Bei Bedarf können sie in jedem Winkel gebogen werden, wobei das Werkzeug auf beiden Seiten direkt in der Nähe der Biegung festgeklemmt wird. Wenn Sie gleichzeitig versuchen, die Stricknadel zu biegen, während Sie die Enden in einiger Entfernung halten, springt sie!
Ich bog einen Federhaken aus einer Speiche. Dafür habe ich ein paar kleine Zangen benutzt:
Manchmal hat es geholfen und groß)))
Wir führen den Haken nicht in das dafür vorbereitete Loch ein ... Zuerst müssen Sie die beiden Hälften des Produkts mit einer Achse verbinden. Ich habe beschlossen, die Achse aus derselben Stricknadel herzustellen:
Nachdem ich die Stricknadel eingesetzt hatte, schnitt ich sie mit einem „Schleifer“ ab und legte das Produkt mit einer Seite auf einen spontanen Amboss (dessen Rolle ein Stück Stahlblech spielte, das früher eine Schablone war)))) und nietete die Enden leicht mit sauberen Hammerschlägen.
Jetzt müssen Sie die Feder installieren. Aber zuerst musst du für sie "einen Platz machen".)))
Nachdem ich einen Marker in das Federloch eingeführt und den Riegel „geöffnet“ habe, habe ich an der Stelle, an der die Enden des Federhakens von innen herausragen, eine Markierung gezeichnet:
Jetzt entfernen wir die Seitenwände des unteren Elements vom Schleifer, beginnend von dieser Markierung bis zum Ende. Wir setzen eine Hakenfeder ein, wir bohren Befestigungslöcher für Schrauben ...
Das ist alles. Es bleibt ein "Partner" zu machen - ein Haken, an dem sich der Federhaken verfängt. Ich habe lange nicht über die Wahl des Materials nachgedacht - ich habe beschlossen, es aus derselben Dose zu machen.))).
Ich schneide einen Streifen aus den Resten des Gehäuses und fange einen Teil der Ecke ein - es wird nicht weh tun))):
Eine Zange bog vorsichtig ein Ende:
Und gebohrte Befestigungslöcher für Schrauben (Nägel):
Hier ist unser Produkt tatsächlich komplett fertig:
Zu diesem Zeitpunkt begann ich zu überprüfen. Zu diesem Zweck habe ich den Haken mit „Schuh“ -Nägeln an einen Holzblock genagelt und eine Klammer darauf gelegt. Ich habe den Abstand geschätzt, in dem der Estrich selbst befestigt werden sollte:
In dieser Position habe ich es mit demselben Nagel fixiert, danach habe ich es vollständig geschlossen:
Es schloss sich mit einem leichten, leicht wahrnehmbaren „Klicken“. Das heißt, ganz am Ende zog die Feder (deren Rolle der Hakenhaken ist) den oberen Teil leicht nach unten. Also eigentlich sollte es !!
Aber dann stellte sich heraus, dass es ziemlich substanziell ist, "kann nicht"!))))). Beim Versuch, es zu öffnen, wurde ich mit der Tatsache konfrontiert, dass es sehr schwierig ist, es aufzuheben. Das Aluminiumprofil zu fest auf die Basis gedrückt ...
Ich habe dieses Problem ganz einfach gelöst - ich habe die Endzange nur leicht nach oben gebogen. (Nun, das aus Aluminium!))))
Jetzt ist es sehr bequem, es zu öffnen und leicht einen Finger zu hebeln.
Ich bog es, stupste es ein wenig an, also räumte ich mit einer runden Feile diesen Ort auf:
Auf dem Foto scheint es mir nur schlechter gegangen zu sein!)))). Aber es wurde einfach von Kratzern eines Blitzes reflektiert ... Eigentlich sind diese Kratzer nicht so sichtbar und werden leicht durch Farbe verdeckt.
Lackieren - der nächste (und letzte) Herstellungsschritt:
Ich habe genau das Produkt bekommen, das ich wollte. Mit den gleichen Eigenschaften, aber viel kleiner:
Jetzt kann ich es installieren. Und es dauerte nur zwei Stunden, um drei dieser Befestigungselemente herzustellen! Und das nächste Mal werde ich mich in viel kürzerer Zeit treffen, da ich nicht jeden Prozess schrittweise fotografieren werde.)))
Alles Gute! Auf Wiedersehen! Ich hoffe, jemand findet diese Beschreibung hilfreich!