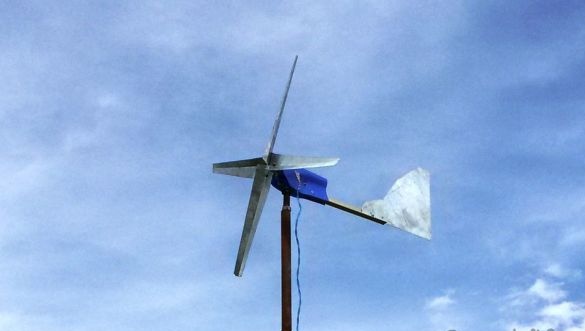
Um die hergestellte wiederaufladbare LED-Lampe mit Strom zu versorgen, Beschreibung davon Auf der Website wird ein Windgenerator hergestellt, der auf einem Gleichstrommotor (24 V / 0,7 A) mit Permanentmagneten basiert und derzeit verwendet wird. Der Windgenerator liefert unter durchschnittlichen Wetterbedingungen abhängig von der Windgeschwindigkeit eine Ausgangsspannung von 0,8 bis 6,0 Volt und einen Strom von bis zu 200 mA. Anschließend wandelt ein stabilisierter Spannungswandler diese Ausgangsgleichspannung vom Windgenerator in die erforderliche Gleichspannung um, die ausreicht, um die Batterie aufzuladen oder die erforderliche Last zu liefern.
Der vorgeschlagene Windgenerator ist einfach herzustellen, erfordert keine genauen Berechnungen und Herstellung komplexer Teile, die Anschaffung teurer Komponenten. Neben der im obigen Artikel betrachteten Variante kann ein solcher Windgenerator auch andere Anwendungen finden. Wir verwenden es dort, wo möglicherweise eine kleine Menge Strom benötigt wird, um ein Gerät mit geringem Stromverbrauch mit Strom zu versorgen. Zum Beispiel für den Betrieb einer kompakten Wetterstation, zur Überwachung des Wasserstandes in einem Tank, zur Notbeleuchtung und zur Steuerung der Automatisierung eines Gewächshauses. Tagsüber erhält der Akku des Geräts mit Wind bei Wind die freie Windenergie und gibt sie zum richtigen Zeitpunkt an den Verbraucher weiter. Natürlich ist die Windenergie, die zu uns kommt, nicht großartig, aber sie kommt fast ständig zu uns. Und wenn Sie ein Gerät für seine Akkumulation und Verwendung machen mit seinen eigenen HändenAus improvisierten Materialien ist diese Energie dann frei und das Gerät ist außerdem wirtschaftlich, kompakt, mobil und nichtflüchtig.
In diesem Artikel wird vorgeschlagen, einen Windgenerator aus einem Gleichstrommotor herzustellen.
Einen Windgenerator bauen.
1. Die Wahl des elektrischen Generators.
Zur Verwendung als Generator mit geringem Stromverbrauch für das Gerät können Sie den fertigen Schrittmotor unverändert verwenden. Für maximale Leistung ist es nach Möglichkeit ratsam, einen Motor mit möglichst geringem Festkleben der Welle und mit möglichst vielen Schritten pro Umdrehung zu verwenden. Eine Variante der Umwandlung eines Elektromotors oder Anlassers in einen Generator ist möglich. Im Internet werden verschiedene Nacharbeitsoptionen beschrieben.
In unserem Fall wurde die einfachste Option gewählt.Als elektrischer Generator verwenden wir einen Gleichstrommotor (24 V / 0,7 A) mit Permanentmagneten, für den keine Änderungen erforderlich sind. Es hat die Eigenschaft der Reversibilität - wenn sich seine Welle dreht, erscheint Spannung an den Motorkontakten. Dieser Elektromotor wurde aus einer moralisch veralteten Rechenmaschine entfernt.
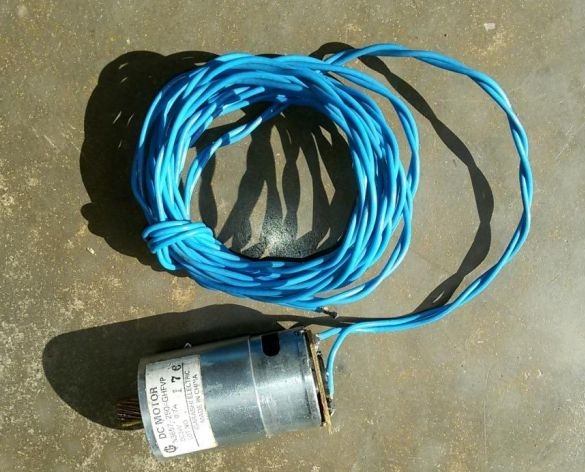
2. Die Wahl des Propellerdesigns.
In der ersten Version des Entwurfs des Windgenerators wurde zur Vereinfachung der Herstellung der Kunststoffpropeller mit einem geeigneten Landedurchmesser von einem Industrieventilator als Grundlage für den Propeller verwendet. Um das Drehmoment auf der Generatorwelle zu erhöhen, wurde die Länge ihrer Schaufeln mit dünnwandigen Metallplatten mit einem Profil nahe dem Original hinzugefügt.
Dieses Propellerdesign schlug jedoch fehl. Bei starkem Wind wurde aufgrund der geringen Steifigkeit des Kunststoffpropellers die Metallauskleidung der Blätter nach hinten abgelenkt und traf auf den Strukturständer, was schließlich zum Versagen führte.
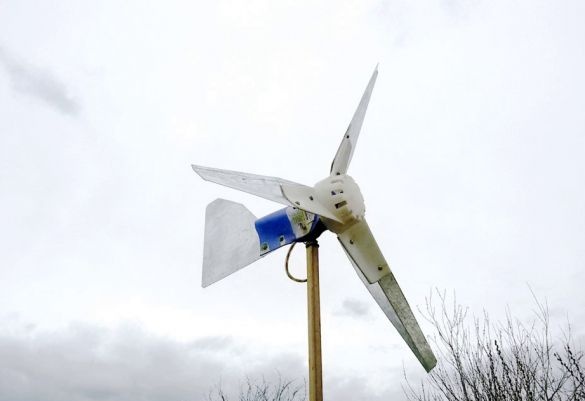
Bei der Ausarbeitung der ersten Option habe ich mich für das Design des technologischen Profils der Klingen und deren Länge entschieden. Diese Propellerparameter beeinflussen die Empfindlichkeit gegenüber schwachen Winden und sie setzen sich durch. Es ist notwendig, dass der Propeller bei etwas Wind das Anhaften der Welle (Anziehung der Statormagnete) überwinden und mit der Drehung beginnen kann.
3. Die Herstellung des Propellers. Wir wählen oder fertigen eine Nabe zum Einbau und Anbringen von Propellerblättern.
In unserem Fall handelt es sich um einen Aluminiumflansch (4 mm dick, Außendurchmesser 50 mm) mit einer axialen Bohrung entlang des Durchmessers der Motorausgangswelle (8 mm - ein Zahnrad wird auf die Welle gedrückt, 10 mm lang) und vier gleichmäßig verteilten M4-Löchern zur Montage der Schaufeln. Installieren Sie zur Befestigung der Nabe auf der Welle eine oder zwei M4-Schrauben (siehe Foto).
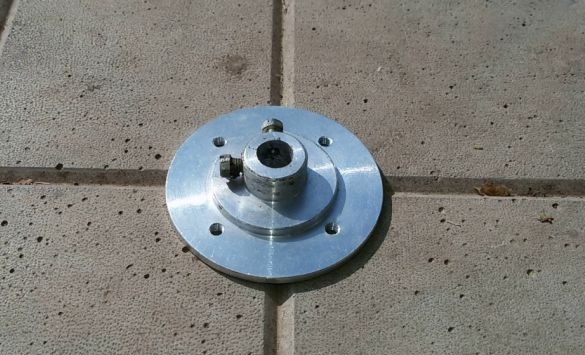
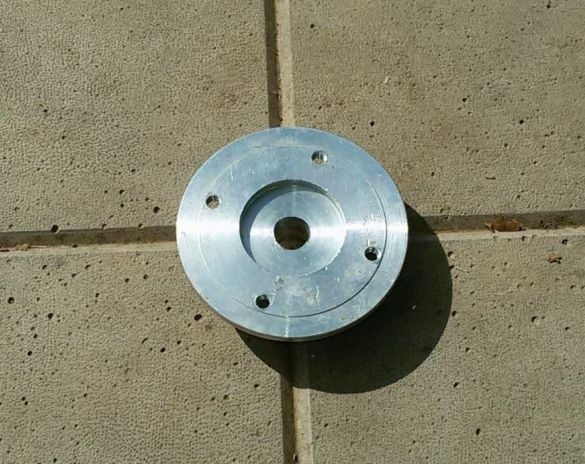
4. Herstellung von Propellerblättern.
Aus einem verzinkten Blech mit einer Dicke von 0,4 bis 0,5 mm schneiden wir 4 Werkstücke in Form eines gleichschenkligen Trapezes: Höhe 250 mm, Basis 50 mm, Oberseite 20 mm. Wir biegen die Klingen in einem Winkel von 45 Grad entlang der Höhe des Trapezes (wodurch eine Versteifungsrippe entsteht) in zwei Hälften (siehe Foto). Wir stumpfen scharfe Kanten und Ecken ab (zu unserer Sicherheit).
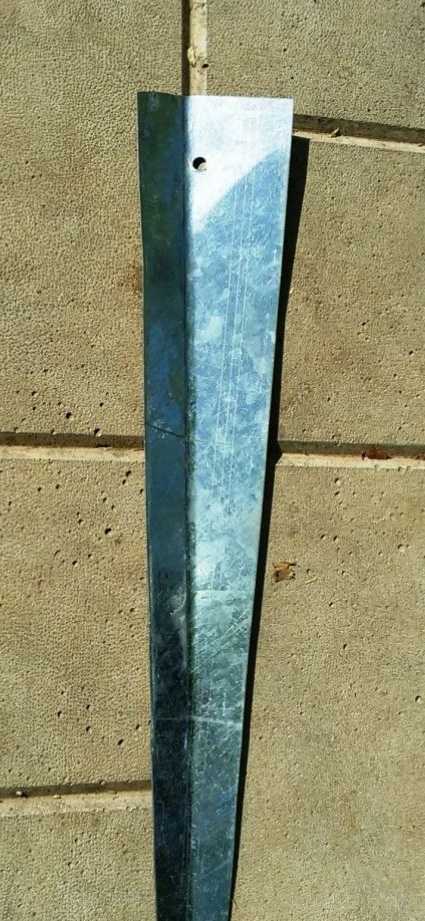
5. Einbau und Befestigung der Propellerblätter.
Wir positionieren die Klinge so auf der Nabe, dass der Biegepunkt auf der Basis über der Achse der Nabe liegt und die angrenzende Hälfte der Basis über dem Befestigungsloch der Nabe liegt (siehe Foto). Wir markieren und bohren ein Loch in die Klingen für eine benachbarte Befestigungsschraube mit einem Durchmesser von 4,2 mm. Wir befestigen die Propellerblätter einzeln mit den Schrauben.
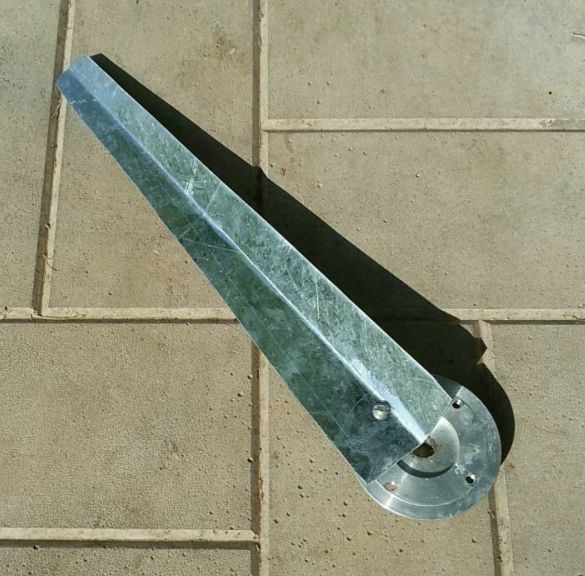
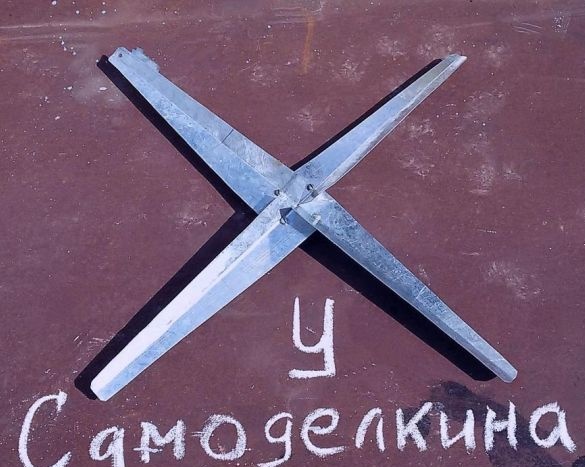
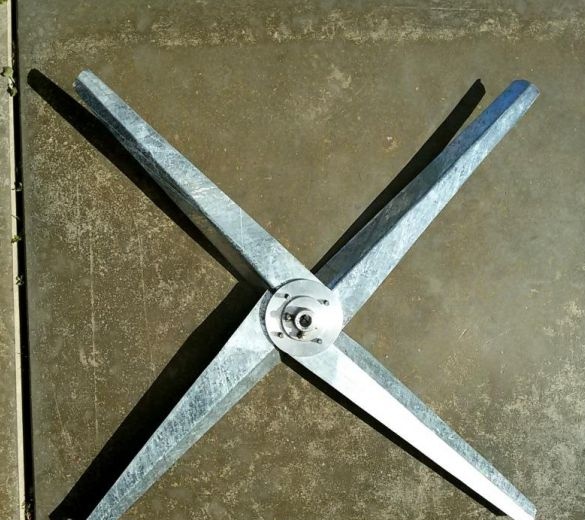
6. Propellerausgleich.
Wir führen ein statisches Auswuchten des Propellers durch. Dazu installieren und befestigen wir den Propeller auf einer kalibrierten (polierten) Stange mit einem Durchmesser, der dem Durchmesser der Motorausgangswelle entspricht. Wir legen die Stange mit dem Propeller auf zwei horizontal kalibrierte Stangen in Höhe des Lineals (Musterflächen) an den Enden der Stange. In diesem Fall dreht sich der Propeller und eines der Blätter fällt aus. Wir drehen den Propeller eine viertel Umdrehung und wenn sich das gleiche Blatt wieder abgesenkt hat, muss es leichter gemacht werden, indem ein schmaler Metallstreifen von der Seite des Blattes abgeschnitten wird. Wir wiederholen einen ähnlichen Vorgang, bis die Stange mit dem Propeller nach dem Einbau in einer beliebigen Position nicht mehr aufhört, sich zu drehen.
7. Herstellung des Flügelteils des Windgenerators.
Wir schneiden das Aluminiumquadrat 20 x 20 mm auf eine Länge von 250 mm. Auf einer Seite des Quadrats installieren wir für eine oder zwei Schrauben (Nieten) einen vertikalen Stabilisator in Windrichtung.
Auf der anderen Seite des Platzes installieren und befestigen wir eine Klammer an zwei Schrauben, um den Motor - Generator zu sichern. Die Klemme und der Stabilisator bestehen ebenfalls aus verzinktem Blech mit einer Dicke von 0,4 bis 0,5 mm (Korrosionsschutzmaterial ist möglich). Die Länge der Klemme entspricht der Länge des Motors. Die Länge des Stabilisators beträgt ca. 200 mm, die Form entspricht dem Geschmack des Herstellers.
Befestigen Sie die Stange auf der unteren Ablage des Quadrats in der Mitte der Klemme fest (es ist wünschenswert, für ihren Korrosionsschutz zu sorgen), um die Struktur im Rohr der Windgeneratorstrebe zu installieren. Die beste Option zur Bestimmung der Position dieser Stange besteht darin, den Schwerpunkt einer vormontierten und vollständig montierten Struktur zu bestimmen und anschließend Löcher zu bohren, um die Stange dort zu befestigen.

8. Montage des Windgenerators.
Wir installieren den Motor - Generator und befestigen ihn mit einer Klammer. Wir befestigen den Propeller an der Motorausgangswelle. Um den Generator vor atmosphärischen Niederschlägen zu schützen, schneiden wir einen Schutzzaun aus einer geeigneten Plastikflasche aus und installieren ihn. Befestigen Sie es mit einer Schraube.
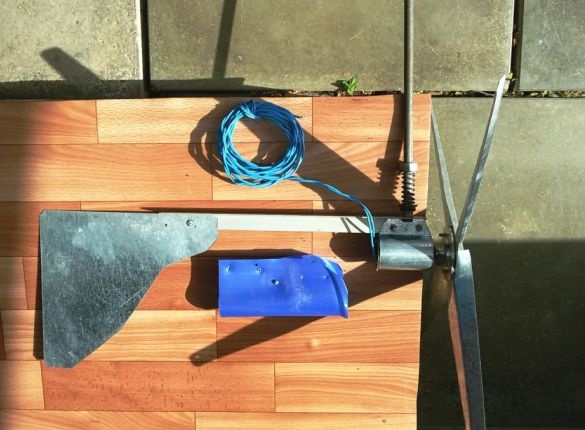
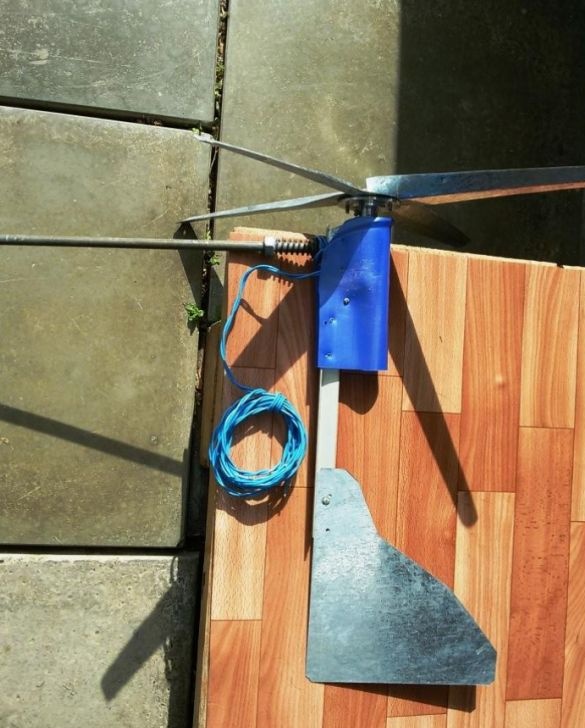
9. Debuggen eines Windgenerators.
Installieren Sie den zusammengebauten Windgenerator in einem offenen Bereich in Windrichtung vor. Wir bilden ein variables Profil der Klingen. Wir biegen den gebogenen Teil der Schaufeln so, dass an den Enden der Schaufeln (schmaler Teil) der Gliedmaßenwert 10 ... 15 Grad beträgt (minimaler Luftwiderstand bei maximaler Umfangsgeschwindigkeit der Schaufeln). In der Mitte des Propellers variiert die Größe des Gliedes am Blatt zwischen 30 und 45 Grad. Mit zunehmendem Biegewinkel nimmt die Empfindlichkeit des Windgenerators gegenüber dem Wind zu, aber aufgrund der Zunahme des Widerstands nimmt die Generatordrehzahl ab, was zu einer Abnahme der Leistungseigenschaften führt. Daher wählen wir durch Ändern des Winkels der Schaufel das optimale Profil im Wind.
10. Installation eines Windgenerators.
Um einen Windgenerator zu installieren, wird ein Gestell mit der erforderlichen Höhe (vorzugsweise über den umgebenden Bäumen) aus einem Rohr (Wasser) hergestellt und am Objekt befestigt. Die Montagestange des Windgenerators muss sich im Rohrgestell frei drehen können. Vor dem Einbau wird nacheinander eine sequentielle Unterlegscheibe auf die Windgeneratorwelle aufgebracht - eine Zwischenscheibe zur Erleichterung der Drehung, eine Spiralfeder zum Ausgleich des Restungleichgewichts des Propellers und eine Schutzscheibe zum Verringern des Eindringens von Niederschlag in das Zahnstangenrohr (bei dieser Ausführung ist eine Mutter geeigneter Größe installiert).
Der Draht vom Generator wird mechanisch vom Kontaktbruch fixiert, senkt sich entlang des Racks mit einem Längenrand zum möglichen Verdrehen um das Rack und einer obligatorischen Schleife zum Tropfen von Niederschlagstropfen vor dem Eintritt in den Verbraucher.
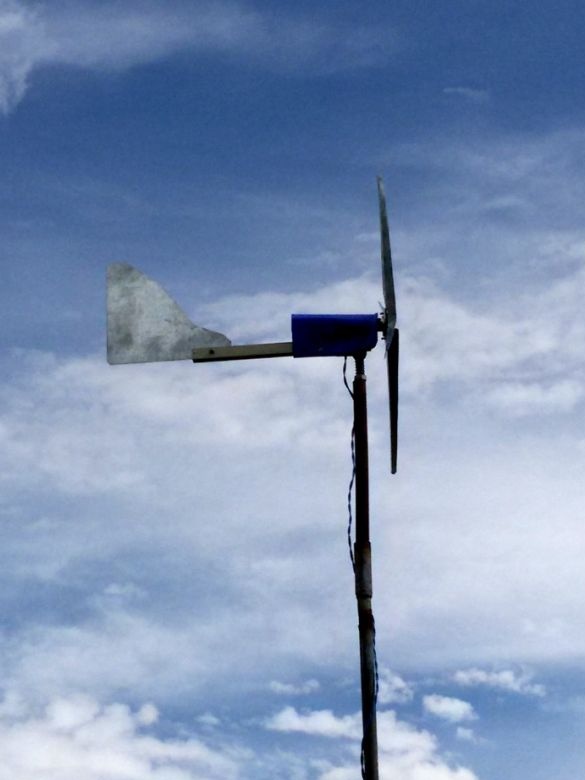
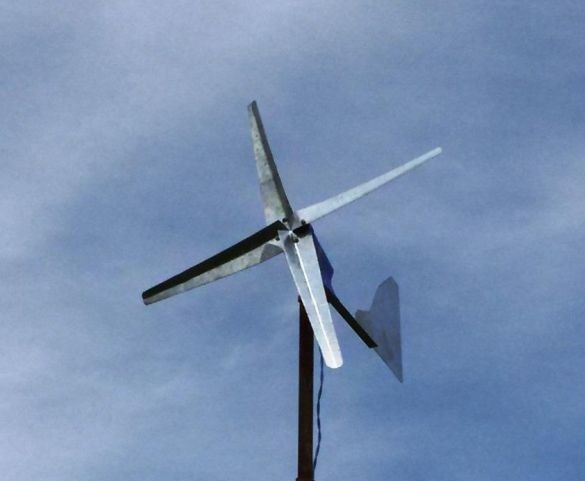