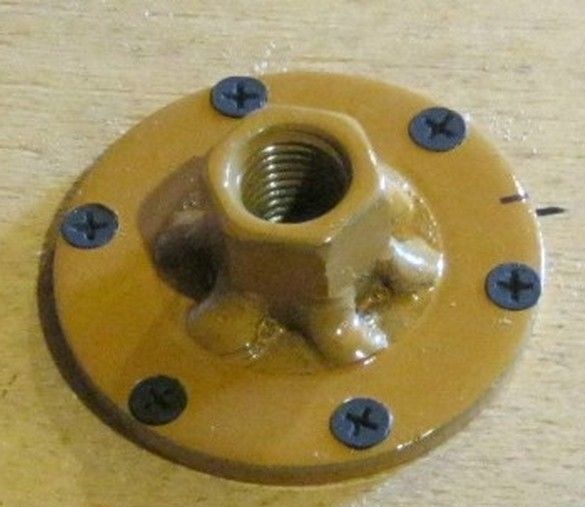
Konstruiert haben HolzdrehmaschineIch hatte Spaß mit dem einfachen Drehen in den Zentren. Nach einer Weile wurde es notwendig, vielfältigere Werkstücke zu verarbeiten. Ich musste mein Gehirn wie aus improvisierten Mitteln bewegen, ohne Zugang zu einer Drehmaschine eines Drittanbieters (für Metall), um die entsprechende Ausrüstung herzustellen. Eines der Designs erwies sich als sehr kostengünstig, praktisch und gefragt.
Die Schnappvorrichtung bestand häufig aus zwei Teilen - einer universellen kleinen Metallfrontplatte und einem speziellen Holzteil. Wie üblich kann auch eine Metallfrontplatte verwendet werden, indem Schrauben am Werkstück befestigt werden.
Was wurde verwendet.
Werkzeuge
Die Holzdrehmaschine selbst, Fräser dafür, ein Satz Bankwerkzeuge. Auf eine Schneidemaschine (Schleifmaschine) kann man nicht verzichten, es ist besser, eine kleine zu verwenden - sie ist bequemer und sicherer. Kopfhörer für Aufnahmen und Schutzbrillen oder Visiere. Steigen Sie auch nicht ohne Schweißen aus - ein kleiner Wechselrichter und Zubehör. Elektroden 2,5 mm. Oft verwendete Schmelze. Es ist notwendig, weder zu bohren, bequemer und genauer zu sein, es ist klar, die Maschine.
Material.
Eigentlich nur die richtige Anzahl von Muttern und Unterlegscheiben. Es ist besser, das fertige Metallstück zu lackieren, als die Lackierung. Als kleiner Baum für "enge Spezialisierung" verwende ich oft trockenes Birkenholz mit gleichmäßigen Schichten.
Also. Die Spindel meiner Drehmaschine endet mit einem M16-Gewinde, das die Verwendung von Standardhardware ermöglicht. In diesem Fall handelt es sich um eine "Verlängerungsmutter". Es wird direkt an der Maschine halbiert, eingeschaltet und rotierend. Winkelschleifer. Es sollte sorgfältig geschnitten werden. Probieren Sie es zunächst an einer ausgeschalteten Maschine und mit einem Leerlaufschleifer in den Händen vorsichtig an, damit es praktisch ist, wo immer sich Ihre Ellbogen befinden und nicht in rotierende Teile passen.
Die Maschine schaltet sich ein und nachdem wir eine vorab getestete Pose eingenommen haben, die von einer Mühle eingeschaltet wurde, treffen wir eine Markierung auf der Markierung in der Mitte der rotierenden Mutter. Zuerst besonders vorsichtig, bis die Kanten gesägt sind, dann beginnt es gleichmäßiger zu schneiden und der Druck kann leicht erhöht werden.
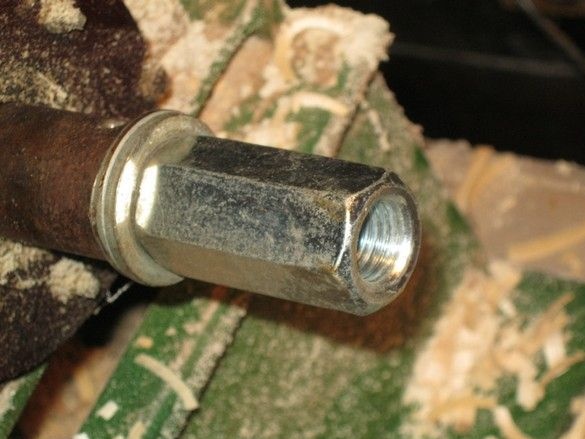
Nach einiger Zeit unserer Bemühungen wird die Wand der Nuss durchgeschnitten und die Hälfte fällt ab.Die Höhe jeder Hälfte ist unter Berücksichtigung der Breite des Schnitts etwas größer als die der Standardschwester ohne „Verlängerung“. Die Länge des Gewindes auf der Spindel meiner Maschine erlaubt nicht die Verwendung einer normalen Mutter - sie ragt unter der fertigen Frontplatte hervor und verursacht später beim Arbeiten viele Unannehmlichkeiten.
Der nächste Schritt ist das Schweißen. Aus dem Standard-Hardware-Sortiment nehme ich eine „verstärkte Unterlegscheibe“, in einigen Geschäften wird sie als „Unterlegscheibe“ mit geeignetem Durchmesser bezeichnet. Normalerweise ist dies fast das größte verfügbare Sortiment. Sie müssen überprüfen, ob die Mutter hineinfällt. Die Mutter sollte in der Mitte des Lochs in der Unterlegscheibe stehen. Eine geschnittene Mutter hält besser - auf einer Seite befindet sich keine Fase. Dies sollte beim Anprobieren einer neuen Mutter im Laden berücksichtigt werden.
Die abgeschnittene Hälfte ist mit der Unterlegscheibe verschweißt. Ordentlich. Es ist sehr gut, sie zuerst mit einer Klammer festzuziehen, aber normalerweise fällt es ziemlich gut aus. Die Rippen werden in der folgenden Reihenfolge geschweißt - beliebig, dann umgekehrt. Das Werkstück dreht sich um 90 Grad, wieder eines der beiden, dann das Gegenteil. Es besteht also eine geringere Wahrscheinlichkeit, dass die Mutter von der Unterlegscheibe rutscht. Eigentlich habe ich in den ersten Kopien versucht, eine „Nut“ mit demselben Schleifer auf der rotierenden Hälfte der Mutter zu organisieren, um einen sicheren Sitz in dem Loch zu gewährleisten, aber der Winkelschleifer ist nicht das Werkzeug, das diese Aufgabe gut erledigen kann - oft wegen der nicht sehr gleichmäßigen Kante der „Nut“. Die Mutter war nicht sehr auf die Unterlegscheibe ausgerichtet.
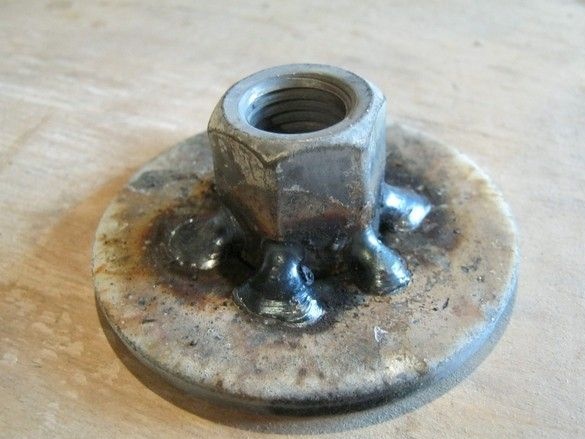
Nach dem Abkühlen des Werkstücks umhüllen wir wie gewohnt die Glaskruste der Schlacke und legen das Werkstück auf die Maschinenspindel. Während der Drehung bewerten wir den Rundlauf. Wenn sie innerhalb angemessener Grenzen liegen, korrigieren wir den mitgelieferten Winkelschleifer.

Es ist für die Ästhetik und auf der Rückseite möglich. Hier notieren wir beim Schärfen mit einem Bleistift an der richtigen Stelle des rotierenden Werkstücks den Durchmesser, entlang dessen die Löcher gebohrt werden. Um die zukünftige Frontplatte mit relativ großen Objekten zu verwenden, können sie mehr gebohrt werden, bis zu sechs, wenn für Kleinigkeiten - drei, vier.
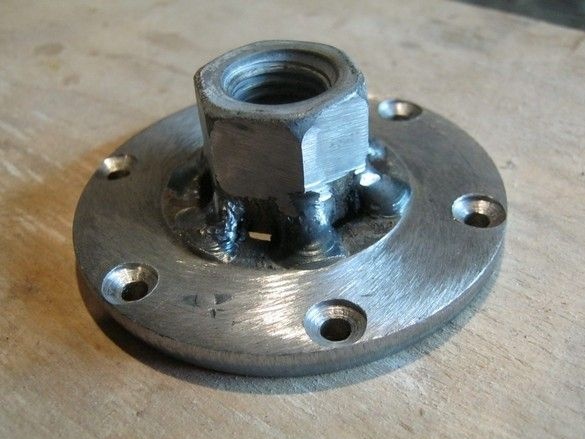
Danach wäre es schön zu malen, bis es Rost gibt - die Zinkschicht ist teilweise verbrannt, teilweise entwässert. Unten knallte "Ocker" aus einer Spraydose in zwei Schichten, obwohl ich normalerweise faul bin.
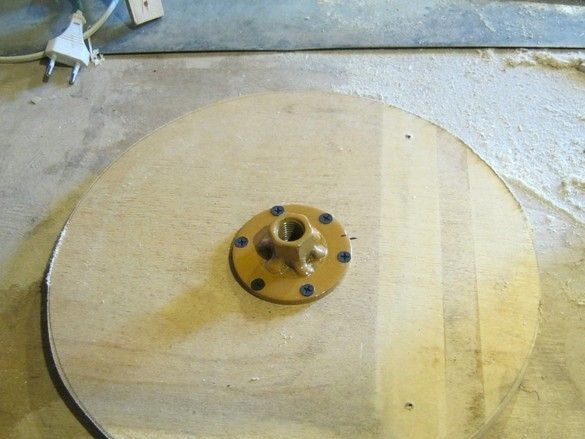
Auf dem Foto besteht die fertige Frontplatte auf der Schleifscheibe aus dickem Sperrholz. Auf einer unter Unterdrückung stehenden Scheibe wird PVA-Kleber mittelgroß auf Schleifbasis geklebt. Durch eine Zeitungsschicht, damit Sie den geleckten Schweiß abreißen können.
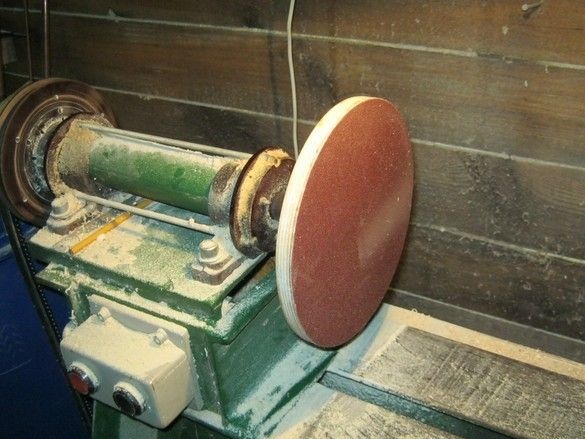
Zum Schärfen des Werkzeugs vor dem Kleben kleine Holzstücke anbringen.
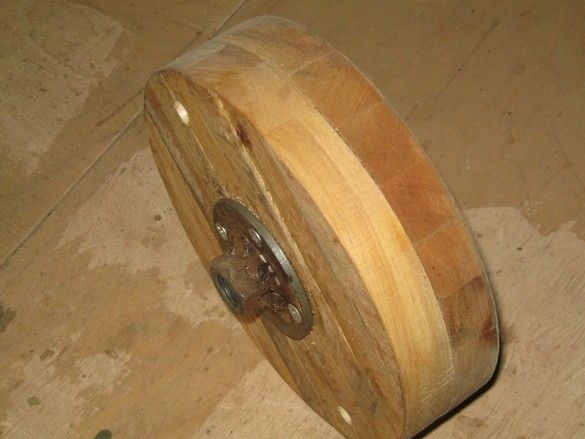
Ein ähnlicher Apparat, aber kleiner im Durchmesser und aus Birkenblöcken in zwei Schichten mit Überlappung geklebt. Zum Schärfen von Drehwerkzeugen. Am Ende befindet sich das gleiche Sandpapier, ein Ledergürtel wird entlang des Umfangs geklebt, um eine Feinabstimmung mit GOI-Paste vorzunehmen.
Und schließlich die Verwendung unserer Frontplatte für die aktuelle Arbeit. Wie das übliche ist unser kleines Gerät praktisch dort zu verwenden, wo Sie das Werkstück an einer Kante ohne hintere Mitte montieren müssen. Gleichzeitig ist es sehr bequem, das Werkstück auf den Zwischenblock zu kleben. Ein Stück der Platte wird nicht mit langen Schrauben befestigt und auf einen geeigneten Durchmesser gedreht, das Werkstück ist bereits darauf geklebt. Schmelzklebstoff.
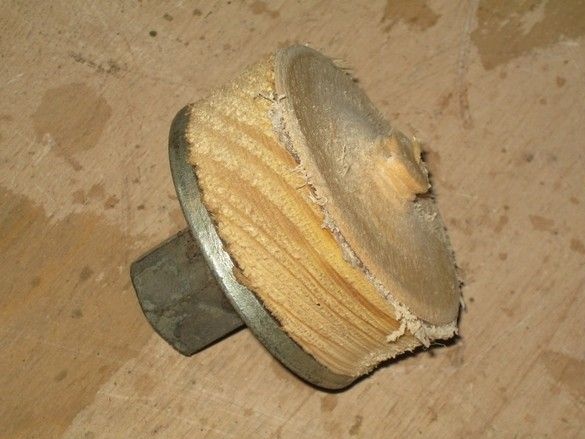
Auf dem Foto befindet sich eine solche "Patrone", bei der ein Zuschnitt vom Werkstück übrig bleibt. Vor dem Verkleben des nächsten wird die Frontplatte in die Maschine eingesetzt und mit einem Schneidwerkzeug „geschnitten“, wobei die Reste des geklebten abgeschnitten werden. Gleichzeitig ist es notwendig, einen Teil der alten Klebeschicht einzufangen, damit sich dieser (Kleber) nicht zu stark ansammelt.
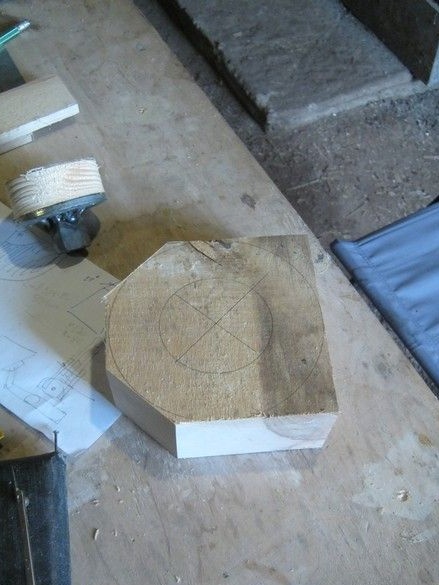
Das Werkstück ist markiert, während unter anderem ein Kompass, ein Kreis mit einem Durchmesser etwas größer als der "Block" auf der Frontplatte gezeichnet ist. Auf diese Weise können Sie es beim Kleben genau ausrichten.
Mit Heißkleber schmiere ich beide zu klebenden Flächen, nicht unbedingt vollständig, ein Umfang um den Umfang reicht aus, einen Zentimeter vom Rand entfernt.
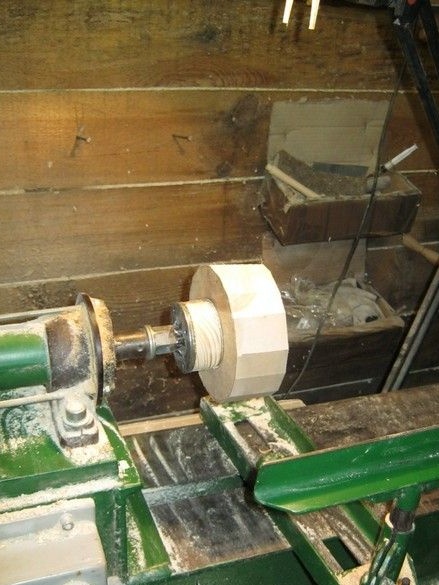
Vor dem vollständigen "Narren" ist es zunächst besser, das Werkstück in die Mitte zu drücken, und es dann zu entfernen, wenn keine Stoßbelastung vorliegt.
Das Schöne an einer solchen Installation liegt im Block, in dem deutlich sparsameren Aufwand des Werkstückmaterials, außerdem müssen Sie sich beim Drehen nicht ständig daran erinnern, wie lang die Schrauben sind, um den Fräser nicht bis in die Tiefe zu klettern.
Nun, zum Nachtisch - es gibt verschiedene Optionen für ein spezielleres Werkzeug, das auf der hergestellten Frontplatte basiert.
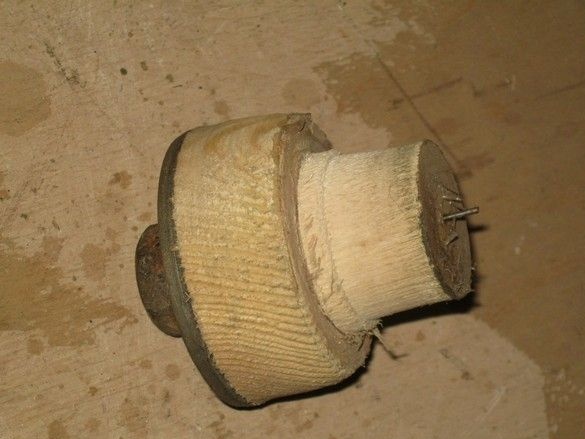
Zum Beispiel war es in diesem Fall erforderlich, dass sich etwas sehr genau um das bestehende Zentrum drehte - so einfach war das.
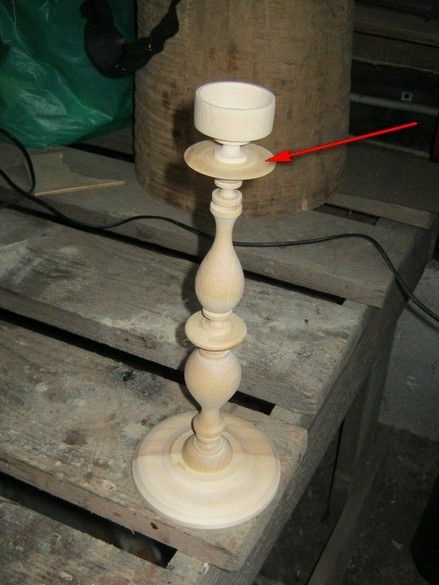
Oder zum Beispiel - ein Teil eines Kerzenhalters aus 6 mm Sperrholz oder einer dünnen Birkenplatte. Für das Spannen und Verarbeiten wurde ein solcher Druckknopf hergestellt.
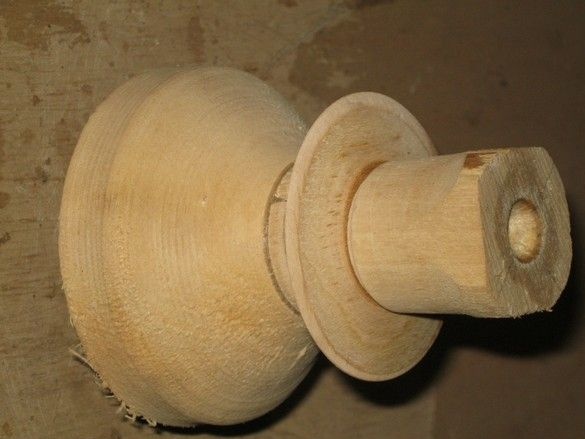
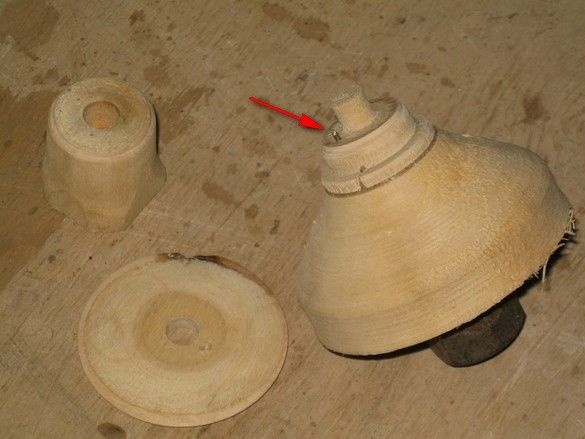
Scharfe Nelken verhindern, dass sich das Werkstück dreht. Zusammengebaut, von der hinteren Mitte festgezogen.
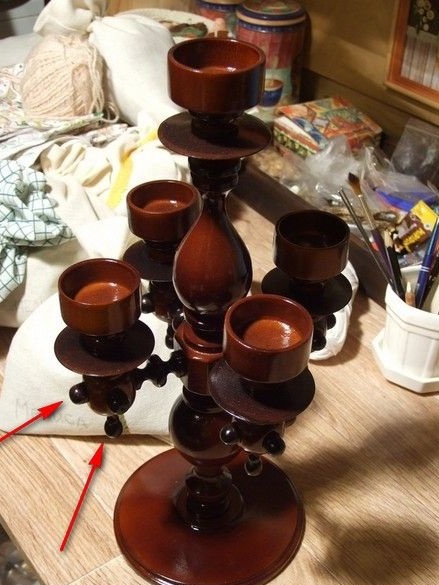
Bei der Herstellung der Kandelaber wurden einige kleine Teile benötigt, wie zum Beispiel Navels. Ich musste eine einfache Spannzange aus Holz herstellen.
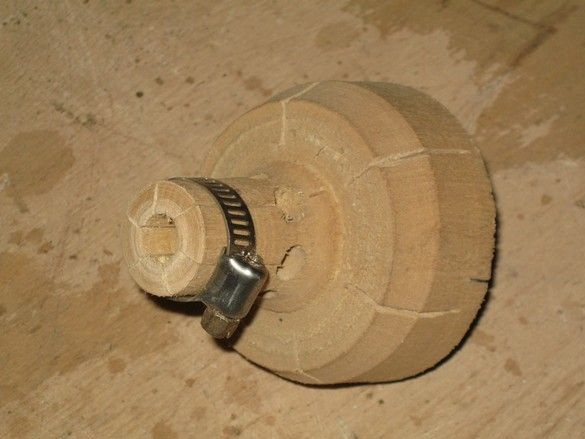
Trotz der etwas eingeschränkten Möglichkeiten hat es auch eine Reihe von Vorteilen, nämlich einfache Herstellung, niedrige Kosten. Bei der Bearbeitung von Miniaturteilen in der Nähe der meisten „Backen“ sollte man keine Angst haben, die „Patrone“ mit einem Werkzeug einzuhaken, was bei Verwendung eines Metallfabrikanalogons manchmal fatale Folgen hat. Ja, die Sicherheit ist wieder ein Minimum an hervorstehenden Teilen. Sie können noch weiter reduziert werden, wenn Sie eine Metallschneckenklemme durch geglühten Stahl- oder Kupferdraht ersetzen oder sogar eine kleine Verjüngung an der Außenseite der Backen vornehmen und den Ring zum Klemmen füllen. Metall oder Holz.
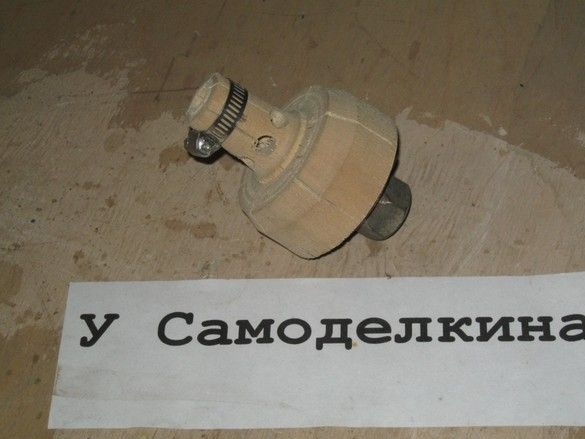
Bei der Herstellung eines Spannzangenfutters wird zunächst der Zylinder gedreht, ein zentrales Loch (eine Bohrmaschine) gebohrt, Löcher markiert und seitlich gebohrt. Dann wird in der Drehmaschine die zukünftige Klammer bearbeitet - es werden nicht dicke Backen gebildet. Zuletzt schnitt er die Spannzangenblätter ab.