In meiner Freizeit mache ich oft meine Lieblingsbeschäftigung - verschiedene elektronische Strukturen zu entwerfen und natürlich, um ein komplettes Gerät zu erhalten, braucht man nur ein fertiges elektronisch Die Schaltung (eine Leiterplatte mit Funkkomponenten, Kabeln usw.) sollte in einem schönen, fertigen Gehäuse untergebracht werden, das das Gerät vor externen negativen Faktoren schützt und das Auge des Besitzers über viele Jahre hinweg erfreut.
Ich denke, viele Funkamateure stimmen mir zu, dass es natürlich möglich ist, je nach Komplexität in wenigen Stunden ein radioelektronisches Design zu erstellen, aber es ist oft sehr schwierig, ein fertiges Gehäuse dafür zu finden, und es wird wertvolle Zeit damit verschwendet, danach zu suchen. Natürlich ist es immer möglich, einen fertigen Koffer zu kaufen, aber es ist Geld, Zeit und nicht immer Qualität. Aus diesem Grund habe ich beschlossen, dass es schneller und zuverlässiger ist, die Gehäuse selbst auf die erforderlichen Größen und aus verschiedenen Materialien herzustellen. Zu diesem Zweck wurde ich als Mini-Kreissäge aus einer elektrischen Bohrmaschine konzipiert - als Option mit den geringsten Kosten.
Material:
- Sperrholz 12 mm;
- Sperrholz 5 mm;
- eine Klemme zur Befestigung von Rohren Dy = 32;
- M16 Haarnadel 200 mm lang;
- Sägeblatt (Innendurchmesser 16 mm, Außendurchmesser 62 mm, Dicke 0,8 mm);
- Lager 6000 RS (26 × 10 × 8 mm)
- Schraube M8 × 35;
- Schraube M4 × 25;
- Nüsse - "Schaf" M4;
- M16-Muttern;
- Unterlegscheiben;
- selbstschneidende Schrauben;
- Faserplatte 5 mm.
Werkzeuge:
- elektrische Bohrmaschine (Basis der gesamten Maschine);
- Schraubendreher;
- Stichsäge;
- Quadrat;
- ein Bleistift;
- Bohrer.
Schritt-für-Schritt-Anleitung zur Herstellung einer Mini-Kreissäge aus einer elektrischen Bohrmaschine.
Die Farm fand ein Stück Sperrholz 12 mm, aus dem die Komponenten der Maschine hergestellt wurden. Die Verwendung von Spanplatten oder Holzbrettern ist ebenfalls möglich. Die einzige Frage sind die Vorlieben, die einfache Verarbeitung und die Verfügbarkeit dieses Materials.
Nachdem ich die Position der Bohrmaschine, der Zahnstangen und des Desktops geschätzt hatte, machte ich das Layout der Komponenten auf einer Sperrholzplatte und schnitt sie mit einer elektrischen Stichsäge mit einer feinzahnigen Säge, um große Späne zu vermeiden.
Die Basis der Maschine hatte Abmessungen von 190 mm × 355 mm.
Um die Achsen der elektrischen Bohrmaschine und der Welle, auf der das Sägeblatt montiert ist, zu kombinieren, habe ich einen zusätzlichen Bereich von 5 mm Sperrholz- und 12 mm Sperrholzabfällen mit den Abmessungen 175 mm × 190 mm auf die Basis geklebt. Für zusätzliche Festigkeit wurde die resultierende Struktur in den Ecken mit vier selbstschneidenden Schrauben zusammengezogen, wobei zuvor Löcher mit kleinerem Durchmesser für selbstschneidende Schrauben gebohrt wurden.
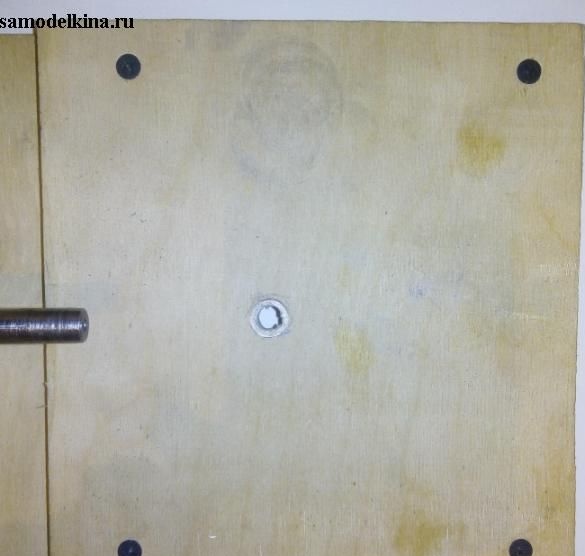
Die Bohrmaschine wird mit einer Rohrschelle Dy = 32 an der Struktur befestigt. Diese Klemme an der Verbindungsstelle mit dem Befestigungsstift hat ein M8-Innengewinde, sodass die Klemme selbst mit einer M8 × 35-Schraube an der Basis befestigt wird (die Länge der Schraube hängt natürlich von der Dicke der Basis mit dem Polster ab).
Gestelle in einer Menge von 2 Stück wurden aus 12 mm Sperrholz mit Abmessungen von 67 mm × 190 mm geschnitten. Angesichts der Konstruktionsmerkmale der Montage des Sägeblattes habe ich die Mitte des zukünftigen Lochs markiert - es stellte sich horizontal 85 mm und vertikal 18 mm heraus. Ich bohrte ein Loch mit einem Stiftbohrer mit einem Durchmesser von 26 mm. Der Durchmesser des Bohrers wurde basierend auf dem Außendurchmesser des Lagers ausgewählt.
Nachdem ich ein Loch für das Lager gebohrt hatte, stellte sich heraus, dass seine Größe 26,5 mm beträgt. Da ich keine Bohrmaschine habe oder nicht für eine Bohrmaschine stehe, habe ich sie mit einer manuellen elektrischen Bohrmaschine gebohrt, daher betrug der Unterschied höchstwahrscheinlich 0,5 mm, und dies war bereits zu viel, um das Lager störend zu montieren. Ich bin sehr einfach aus der Situation herausgekommen - ich habe 0,35 mm dicke Metallstreifen verwendet, um das Lager im Loch abzudichten. Die Streifen wurden mit einer Breite von 12 mm in der Dicke der Pfosten und einer Länge ausgeschnitten, die dem Umfang des Lagers im Außendurchmesser entspricht. Nach diesem Vorgang fielen die Lager mit einer einfach herrlichen Presspassung in Position! Möglicherweise muss dieses Verfahren im Voraus bereitgestellt werden, falls jemand diesen Entwurf wiederholen möchte.
Zunächst wurde beschlossen, Lager mit dem Namen 6000 2RS (in unserem das Modell 100) mit einem Innendurchmesser von 10 mm zur Landung auf einer Welle, die dann bequem in ein elektrisches Bohrfutter eingespannt werden kann (maximaler Durchmesser des Spannfutters beträgt 13 mm). Diese Lager sind geschlossen, was wichtig ist - Feinstaub wird nicht bekommen.
Die Welle zum Landen des Sägeblattes ist vielleicht der schwierigste und kritischste Teil meiner Maschine. Angesichts der Tatsache, dass ich das Sägeblatt von einem Freund absolut frei bekommen habe und es nicht gewählt habe, kommen hier die Abmessungen der zukünftigen Welle her.
Die Haarnadel M16 wurde anhand des Durchmessers des Sägeblattsitzes ausgewählt. Als nächstes muss unter den Abmessungen des Lagersitzes (10 mm) von einer und der zweiten Seite des Bolzens geschliffen werden. Auf der Seite, auf der die Welle in das elektrische Bohrfutter eingespannt wird, auf einer Drehmaschine 60 mm schleifen, auf der zweiten Seite muss die Breite des verfügbaren Lagers geschliffen werden, ich habe 10 mm für Genauigkeit ausgelegt. Viele werden argumentieren, dass sich nicht jeder die Arbeit an einer Drehmaschine leisten kann und dieses Verfahren besondere Fähigkeiten erfordert, so dass das Spiel die Kerze nicht wert ist, aber ich möchte alle vom Gegenteil überzeugen. Die Kosten für die Herstellung einer solchen Welle werden durch die Stabilität der Maschine vollständig ausgeglichen (Vibrationen sind gering, die Schnittgenauigkeit ist hoch). Ich habe auch keine Drehmaschine und auch nicht die Fähigkeiten, damit zu arbeiten (abgesehen von der technologischen Praxis an einer Universität), aber ein bekannter Schlosser hat für mich einen Schaft zu einem symbolischen Preis (ca. 1 USD) bearbeitet, da das Teil nicht schwer auszuführen ist. Wie sie sagen - alles liegt in Ihren Händen, meine Herren!
Das Sägeblatt hat mich, wie ich bereits schrieb, mit einem Außendurchmesser von 62 mm, einem Innendurchmesser (unter dem Sitz) von 16 mm und einer Dicke von 0,8 mm völlig frei gemacht. Feinzahn - zählte nicht die Anzahl der Zähne. Ein kleiner Zahnspalt verhindert, dass das Sägematerial das Sägeblatt einklemmt. Nachdem ich die Position des Sägeblattes auf der Welle geschätzt hatte, stellte ich es richtig ein (die Hauptausrichtung) und klemmte es mit zwei M16-Muttern fest.
Ein Arbeitstisch mit den Maßen 190 × 250 mm besteht aus 5 mm Sperrholz. Die Länge des Schlitzes für das Sägeblatt wird durch seinen Durchmesser bestimmt. Ich habe es ein bisschen mit einem Rand gemacht - 75 mm lang und 5 mm breit. Propyl machte eine elektrische Stichsäge. Ich muss keine kleinen Details schneiden, wie beim Modellieren, daher war dieser Schnitt für mich optimal, obwohl eine Schnittbreite von 2 mm in meinem Fall ausreichen würde. Die Abmessungen des Desktops müssen auf der Grundlage der bequemen Montage der Maschinenwelle im elektrischen Bohrfutter ausgewählt werden.
Montage
Jede Strebe mit eingepressten Lagern wurde mit drei dicken selbstschneidenden Schrauben (5 mm) an der Basis befestigt, um die Steifigkeitsstruktur zu verraten. Der Abstand zwischen den Pfosten betrug 138 mm (axial). Der Desktop wurde an 4 selbstschneidenden Schrauben (3,5 mm) befestigt. Natürlich vorgebohrte Löcher mit kleinerem Durchmesser, um eine Delaminierung des Sperrholzes zu verhindern.
Als Leitfaden benutzte ich einen Holzbalken von 15 × 10 mm, 280 mm lang, der um meine Seite lag und gerade Seiten hatte. Natürlich ist es besser, eine kleine Metallecke zu verwenden, aber ich habe keine gefunden. An den Rändern des Trägers bohrte ich unter Berücksichtigung der Breite des Arbeitstisches 4,1 mm Löcher für M4 × 25-Schrauben, auf denen ich Unterlegscheiben mit breiten Feldern von der Unterseite des Trägers installierte, um den Träger zum Arbeitstisch anzuziehen. Ich habe M4-Muttern zum bequemen Anziehen auf die Schraube gelegt.
Von den Enden der Maschine wurde die zwischen den Gestellen, der Basis und dem Arbeitstisch gebildete Öffnung mit Faserplatten-Segmenten abgedeckt, um ein Verteilen von geschnittenen Produkten im Raum zu verhindern. Einerseits ließ ich die Gelegenheit, das Sägemehl regelmäßig zu reinigen, indem ich die Faserplatte auf die Schrauben legte, andererseits nagelte ich sie mit kleinen Nägeln fest.
Eigentlich Montagemaschine ohne Bohrmaschine
Fazit
Abschließend möchte ich hinzufügen, dass mein Design vollständig für die Materialien und Arbeitswerkzeuge entwickelt wurde, die ich hatte. Jeder, der die Möglichkeit hat, kann die Maschine komplett aus Metall herstellen, was der Maschine nur Stabilität verleiht.
Die Arbeit der Maschine ist reibungslos mit minimalen Vibrationen. Für zusätzliche Sicherheit (wie Sie wissen, ist es nie überflüssig) und Schutz vor unbeabsichtigter Bewegung ziehe ich meine Werkzeugmaschine mit einer provisorischen Klammer auf die Arbeitsfläche. Das Sägeblatt ragt 10 mm über die Seite des Desktops der Maschine hinaus, was genau für meine Anforderungen an Amateurfunk geeignet ist. Die Maschine bei mittleren Umdrehungen einer elektrischen Bohrmaschine schneidet leicht Textolith mit einer Dicke von 2 mm, Faserplatten mit einer Dicke von 5 mm, ich habe noch keine anderen Materialien ausprobiert.
Gut und das Wichtigste! Halten Sie immer die Sicherheitsvorkehrungen ein und Ihre Handwerk wird dir gefallen!