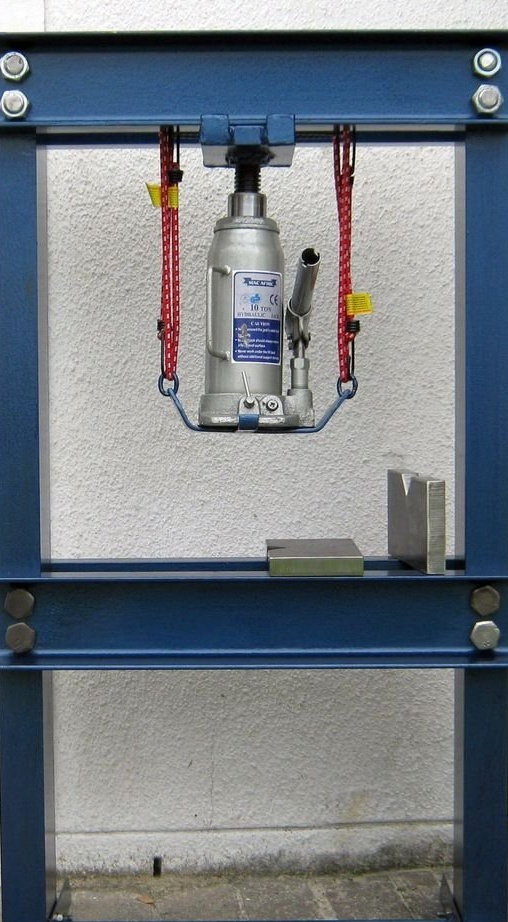
Die Presse ist das Werkzeug, das zu Hause nicht sehr häufig verwendet wird die GarageAber wenn du ihn brauchst, kannst du nicht ohne ihn auskommen.
Der Meister musste die gebogene Fahrradachse begradigen. Dies erforderte eine Presse. Da die Anforderungen minimal sind, sollte die Größe der Presse zwischen der Höhe der Bank und der Bodenhöhe mittelgroß sein.
Er wollte auch, dass der Hydraulikzylinder entfernt wurde, falls er ihn woanders brauchte.
Erster Schritt: Sicherheit geht vor
Am Ober- und Unterarm des Wagenhebers sowie an den Beinen des Stabilisators ist ein geringer Schweißaufwand erforderlich.
In diesem Sinne gelten alle Schweißvorkehrungen: lange Ärmel, geeignete Schweißhandschuhe und ein Lichtbogenschweißhelm. Denken Sie daran, dass es im Nackenbereich zu UV-Verbrennungen kommen kann, die nicht von der Unterseite des Helms abgedeckt werden, insbesondere beim Schweißen von Gegenständen auf dem Boden. Beim Schweißen sind auch geeignete Schuhe (Sicherheitsschuhe oder zumindest Lederschuhe) erforderlich. Es ist schwer, saubere Schweißnähte mit heißen Tropfen geschmolzenen Metalls auf den Zehen zum Tanzen zu bringen.
Aufgrund von Dämpfen wird empfohlen, im Freien zu schweißen.
Es gibt auch viel Schneiden und Schleifen von Metall
Vor diesem Hintergrund ist Augen- und Gehörschutz ein Muss. Ein Winkelschleifer mit einer Schneidscheibe ohne angemessenen Schutz verursacht ein Klingeln in den Ohren und sprüht auch einen riesigen Funkenstrom. Achten Sie auf den heißen Funken, der von der Wand reflektiert wird. Brille tragen.
Ein Paar Arbeitshandschuhe reduziert die auf die Hände übertragenen Vibrationen.
Schritt zwei: Werkzeuge und Materialien
Werkzeuge:
- Schweißvorrichtung;
- eine Bohrmaschine mit einer 20-mm-Bimetallkrone "Blu-Mol", die empfohlene Bohrgeschwindigkeit von 440 U / min.
- Winkelschleifer mit einem Scheibendurchmesser von 115 mm + abnehmbaren und schleifenden Scheiben;
Material:
- Messseitengestelle 2 Stk.;
- Kanal 100x50 mm, Länge 560 mm. für Querstangen 4 Stk.;
- Ecke 30 mm. und eine Länge von 1,2 m als Stütze;
- Querstück 460mm;
- Eine Schraube von 20 mm für Querstücke, 8 Stück;
- M8 Schraube zur Unterstützung, 4 Stk.;
- 10 Tonnen Hydraulikzylinder
- Eine Metallplatte für die obere Halterung der Buchse 200 mmx 100 mm x 20 mm 1 Stk.;
- Flussstahl-Metallplatte für Tretlager
300 mm x 3 mm 1 Stk.;
- Armaturen zur Montage der Halterungen der Rückstellfeder der oberen Halterung 300 mm x 10 mm 1 Stck.;
- V-förmige Blöcke 200 mm x 100 mm x 20 mm 2 Stk.;
Schritt drei: Zusammenbau der unteren Stütze
Ganz am Anfang entschied sich der Meister, die Querhalterung von der Ecke für die untere Stütze zu schneiden und zu schweißen. Um die Größe dieser Ecke zu kennen, musste zunächst entschieden werden, wie lang die Querträger des Kanals sein sollen. Da das Material knapp ist, musste ich anhand der verfügbaren berechnen. Somit stellte sich heraus, dass die Länge der Querträger 560 mm betrug, die Länge der Querhalterung für den unteren Träger beträgt 460 mm.
Vor dem Schweißen des Querträgers des unteren Trägers müssen Löcher zur Befestigung der Seitenpfosten, die aus einem Kanal bestehen, markiert und gebohrt werden. Nach dem Schweißen des Querträgers des unteren Trägers werden die vertikalen Pfosten verschraubt.
Schritt vier: Rahmenmontage
Die Blu-Mol-Bimetallkrone ging leicht durch 8 mm Stahl und blieb auch nach 32 Löchern scharf. Auf der gegenüberliegenden Seite des Metalls bleiben nach dem Bohren scharfe Kanten zurück. Diese Metallspäne müssen vor dem Lackieren mit Winkelschleifern geschliffen werden.
Die Löcher in den Querelementen werden in einem Abstand von 30 mm von den Kanten gebohrt. Der Meister bohrte die Löcher so, dass die Zentren der Löcher einen Abstand von 40 mm voneinander hatten (Breite 100 mm minus 60 mm sollte 40 mm betragen). In der Tat wäre es besser, wenn er sie in einem Abstand von 39 mm voneinander machen würde. Es wäre also bequemer, die Muttern festzuziehen.
Anhänge:
2D-CAD-Datei mit Grundmaßen
Fünfter Schritt: Hydraulikzylinderhalter
Der Meister schweißte ein Stück Rohr an die obere Gleithalterung. Der obere Teil des Hydraulikwagens liegt an diesem Segment an. Dann schweißte er die Armaturen, nachdem er sie zuvor gebogen hatte, um die Rückholfedern zu befestigen, die er immer noch nicht hatte aufnehmen können. Gegenwärtig werden als provisorische Hütten anstelle der Federn Schleppseile installiert, die bisher recht erträglich sind.
Außerdem wurden kleine Ecken entlang aller vier Ecken der Halterung geschweißt. Sie dienen zur Auseinandersetzung mit den oberen Kanälen (Querträgern). So gleitet die obere Halterung.
Das Tretlager besteht aus zwei Metallplatten, die geschweißt und gebogen sind, um die Basis des Wagenhebers zu halten. In die gebogenen Teile der Platten werden Löcher gebohrt, in die Kettenglieder eingesetzt und geschweißt werden. In diese Links werden Rückführungslinks eingefügt, die jetzt vorübergehend aus Gummi bestehen.
Schritt sechs: Testen
Finalisierung der Buchse.
Ich musste den Hydraulikzylinder leicht aufrüsten - den Originalstift am Ventil ersetzen und einen viel längeren einsetzen, um die Verwendung mit den Fingern zu vereinfachen.
Diese Presse biegt leicht 10 mm Bewehrungsstäbe auf einem Autospray, jedoch nur bis zu 90 Grad.
Auch mit dieser Presse wurde die Möglichkeit getestet, Stanzteile aus einem Aluminiumblech der Dose Pepsi herzustellen. Dieses Aluminiumblech hat eine Dicke von 1 mm. Als Form wurden ein verzinkter Draht mit einem Durchmesser von 1,23 mm und eine Gummiplatte mit einer Dicke von 1,6 mm als Substrat getestet.
Aber das dünne Aluminiumblech von Pepsi will an den Nähten reißen. Vielleicht solltest du es mit dickerem Metall versuchen, vielleicht funktioniert es. Alternativ können Sie auch einen dünneren Draht verwenden, der dünner als 1,23 mm ist.